Our Company

Established in 1957, Obara is a Japanese manufacturing company founded in Tokyo, Japan.
Though our development evolved around the ever-expanding automotive industry, we supply a full range of welding equipment for every need. Obara Corporation manufactures a comprehensive range of resistance welding equipment. The quality and reliability of these products have earned a worldwide reputation, synonymous with excellence. Our dedication to quality and a customer-first attitude have won us a prominent place in the market and attracted a wide range of loyal customers.
Products

Discover our main product lines
Services

Explore our exceptional services
Obara Around the World

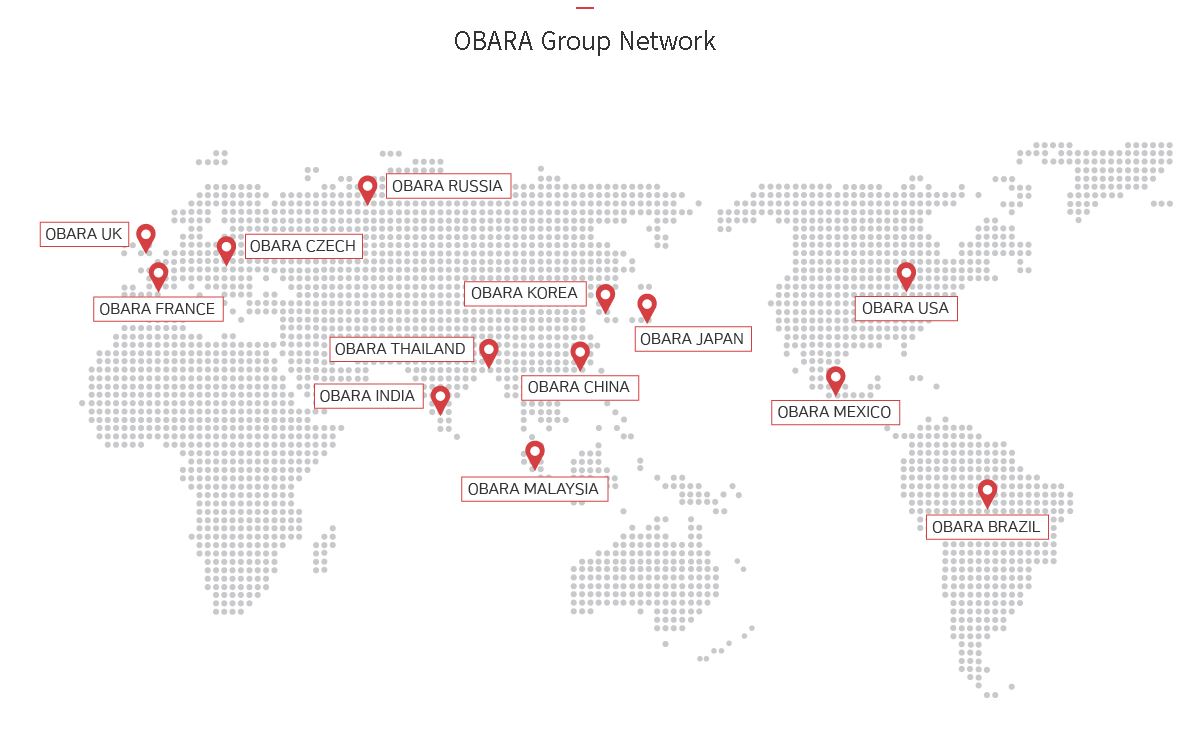
Contact Us

Obara is certified ISO9001 compliant and is ISO14001 certified!